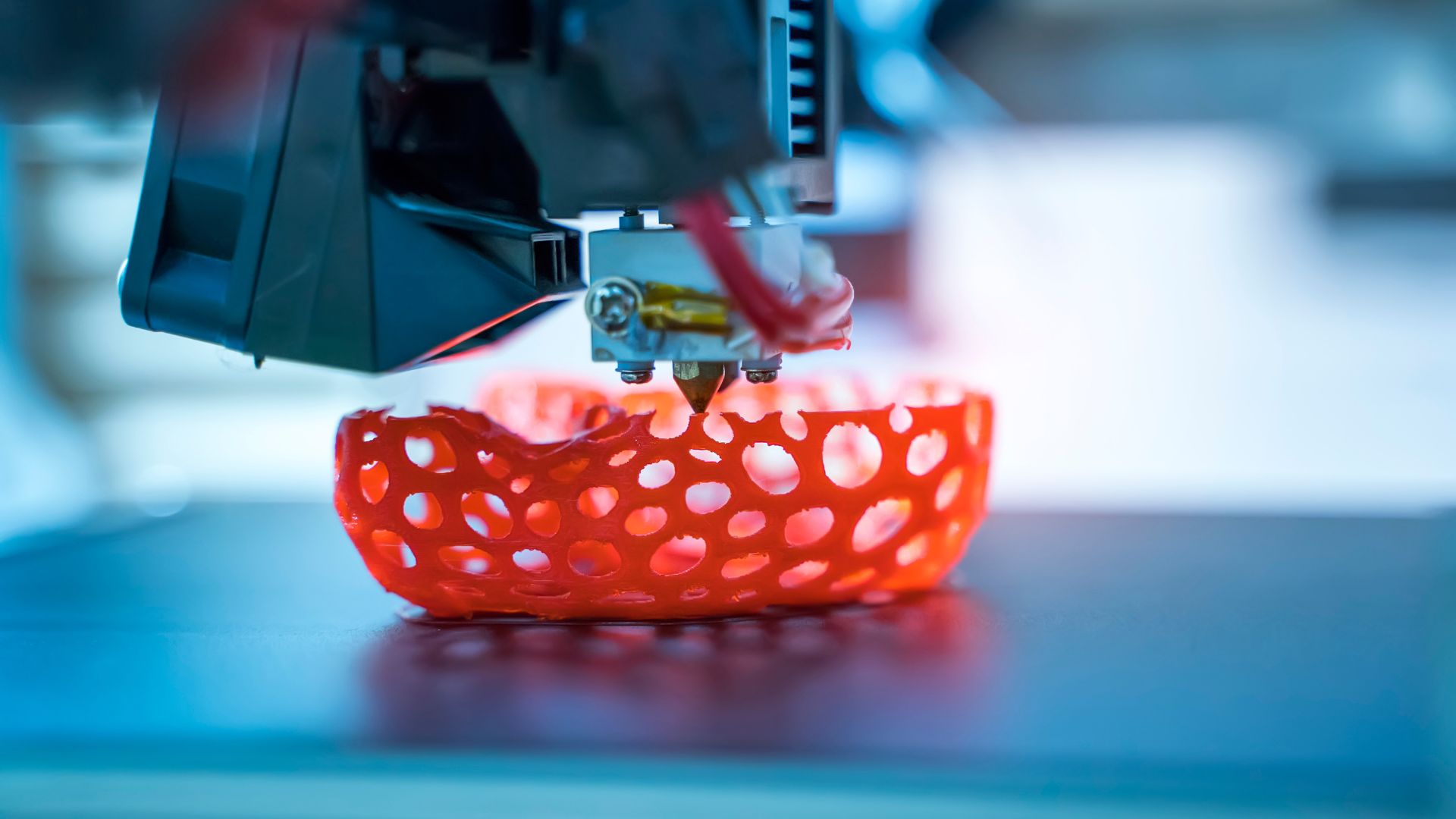
De evolutie van lastechnologie: Van traditionele methoden tot 3D-lassen
Lassen is een van de oudste en meest fundamentele technieken in de metaalbewerking. Wat begon als een eenvoudige manier om metalen aan elkaar te verbinden, heeft zich in de loop der eeuwen ontwikkeld tot een geavanceerde technologie die een cruciale rol speelt in de moderne industrie. De evolutie van lastechnologie heeft geleid tot de ontwikkeling van innovatieve methoden zoals 3D-lassen, die nieuwe mogelijkheden openen voor ontwerp en productie. In dit artikel bespreken we de geschiedenis van lassen, de belangrijkste technologische vooruitgangen en de opkomst van 3D-lassen als de toekomst van deze technologie.
De oorsprong van lassen: Traditionele methoden
Lassen bestaat al duizenden jaren in een of andere vorm. De vroegste vormen van lassen, bekend als smederijlassen, dateren uit de tijd van de Egyptenaren en de Mesopotamiërs, die metalen verwarmden en met hamers samensmeden om verbindingen te maken. Dit was een tijdrovend proces dat hoge temperaturen vereiste en voornamelijk werd gebruikt voor het vervaardigen van wapens, gereedschappen en sieraden.
Met de industriële revolutie in de 19e eeuw nam de vraag naar efficiëntere verbindingsmethoden toe, wat leidde tot de ontwikkeling van nieuwe lastechnieken. Een van de eerste moderne lasmethoden was booglassen, geïntroduceerd aan het eind van de 19e eeuw. Booglassen maakt gebruik van een elektrische boog om hitte te genereren en metalen te smelten, waardoor een sterke verbinding ontstaat. Deze methode werd al snel populair vanwege zijn vermogen om snel en effectief te werken met een breed scala aan metalen.
Een andere belangrijke innovatie in de vroege 20e eeuw was oxyacetyleenlassen, waarbij een vlam werd gebruikt die werd gegenereerd door het mengen van zuurstof en acetyleen. Deze methode bood meer controle over het lasproces en werd veel gebruikt voor het lassen van dunne materialen en voor reparatiewerkzaamheden.
De opkomst van moderne lastechnologieën
Naarmate de industrieën zich verder ontwikkelden, werd de behoefte aan geavanceerdere lasmethoden duidelijk. In de jaren 1930 en 1940 werd TIG-lassen (Tungsten Inert Gas) geïntroduceerd, dat bekendstaat om zijn precisie en schone lassen. Bij TIG-lassen wordt een niet-smeltende wolfraamelektrode gebruikt, terwijl een inert gas zoals argon het lasbad beschermt tegen verontreinigingen. Deze methode wordt vooral gewaardeerd in de lucht- en ruimtevaartindustrie, waar de hoogste kwaliteit en nauwkeurigheid vereist zijn.
MIG-lassen (Metal Inert Gas), ontwikkeld in de jaren 1940, werd een andere belangrijke stap in de evolutie van lastechnologie. Bij MIG-lassen wordt een continue draad als elektrode gebruikt, terwijl een inert gas het smeltbad beschermt. Deze methode is sneller en eenvoudiger te leren dan TIG-lassen en wordt daarom vaak gebruikt in productieomgevingen waar snelheid en efficiëntie van groot belang zijn.
Plasmalassen, geïntroduceerd in de jaren 1960, maakte gebruik van een hoog-energetische plasmaboog om metalen met grote precisie te smelten. Deze techniek werd gebruikt in toepassingen waar een zeer geconcentreerde warmtebron vereist was, zoals in de micro-elektronica en de medische industrie.
De digitale revolutie en automatisering
De laatste decennia van de 20e eeuw zagen een dramatische verschuiving in lastechnologie door de introductie van digitale besturingssystemen en automatisering. Lasrobots werden steeds vaker gebruikt in de auto-industrie en andere massaproductiesectoren. Deze robots, die door computers worden bestuurd, kunnen herhaalde laswerkzaamheden met grote precisie en consistentie uitvoeren, waardoor menselijke fouten worden geminimaliseerd en de productiesnelheid wordt verhoogd.
Met de komst van CNC-machines (Computer Numerical Control) werden complexe laspatronen mogelijk gemaakt door middel van vooraf geprogrammeerde software. Dit stelde bedrijven in staat om met hoge precisie te lassen, wat essentieel was voor de productie van onderdelen voor lucht- en ruimtevaart, medische apparaten en de elektronica-industrie.
De digitalisering van lassen leidde ook tot de ontwikkeling van geautomatiseerde lasinspectiesystemen. Deze systemen gebruiken sensoren en beeldverwerking om de kwaliteit van lassen in real-time te controleren, waardoor defecten onmiddellijk kunnen worden opgespoord en gecorrigeerd. Dit heeft de algehele kwaliteit van laswerk in de industrie aanzienlijk verbeterd.
3D-lassen: De toekomst van lastechnologie
De meest baanbrekende innovatie in de lastechnologie is de opkomst van 3D-lassen of additive manufacturing. Terwijl traditioneel lassen materiaal verwijdert om een verbinding te maken, voegt 3D-lassen materiaal laag voor laag toe om een volledig object te creëren. Dit proces, ook wel bekend als 3D-printen van metaal, opent nieuwe mogelijkheden voor ontwerp en productie die voorheen ondenkbaar waren.
3D-lassen maakt gebruik van een lasboog, laser of elektronenstraal om metaalpoeder of draad te smelten en op een werkstuk te deponeren. De lagen worden opgebouwd volgens een digitaal ontwerp, waardoor zeer complexe structuren kunnen worden gemaakt zonder de beperkingen van traditionele bewerkingsmethoden. Deze techniek wordt steeds populairder in de lucht- en ruimtevaart, medische implantaten, en de auto-industrie, waar op maat gemaakte onderdelen van hoge kwaliteit nodig zijn.
Voordelen van 3D-lassen:
- Ontwerpvrijheid: 3D-lassen stelt ingenieurs in staat om ontwerpen te maken die onmogelijk te realiseren zijn met traditionele methoden, zoals interne kanalen of complexe geometrieën.
- Materiaalefficiëntie: Omdat materiaal alleen wordt toegevoegd waar het nodig is, vermindert 3D-lassen verspilling en maakt het efficiënter gebruik van grondstoffen.
- Snellere prototyping: Ontwerpen kunnen snel worden aangepast en getest zonder de noodzaak van dure gereedschappen of matrijzen.
- Sterkte en duurzaamheid: Omdat 3D-lassen sterke en uniforme verbindingen creëert, kunnen onderdelen die met deze techniek worden gemaakt, dezelfde of zelfs betere mechanische eigenschappen hebben dan onderdelen die met traditionele methoden zijn gemaakt.
Uitdagingen en toekomstperspectieven: Hoewel 3D-lassen veelbelovend is, zijn er nog uitdagingen die moeten worden overwonnen. De technologie is nog relatief duur en vereist gespecialiseerde kennis en apparatuur. Daarnaast zijn er beperkingen in de snelheid van het proces en de grootte van de objecten die kunnen worden geproduceerd. Toch blijft de technologie zich snel ontwikkelen, en er wordt verwacht dat de kosten zullen dalen naarmate de techniek breder wordt toegepast.
De toekomst van 3D-lassen ziet er rooskleurig uit, met voortdurende innovaties die de mogelijkheden verder zullen uitbreiden. Denk bijvoorbeeld aan het gebruik van nieuwe materialen, zoals legeringen die speciaal zijn ontworpen voor additive manufacturing, en de integratie van kunstmatige intelligentie om het proces te optimaliseren.
Conclusie
De evolutie van lastechnologie, van traditionele methoden zoals smederijlassen en booglassen tot de geavanceerde technieken van vandaag zoals 3D-lassen, toont de voortdurende vooruitgang in de industrie. Elke nieuwe stap in de technologie heeft geleid tot verbeterde efficiëntie, kwaliteit en mogelijkheden, waardoor lassen een onmisbare techniek is gebleven in een breed scala aan toepassingen.
Met de opkomst van 3D-lassen staan we aan de vooravond van een nieuwe revolutie in de metaalbewerking. Deze technologie heeft het potentieel om de manier waarop we objecten ontwerpen en produceren radicaal te veranderen, met voordelen die reiken van verminderde materiaalkosten tot ongekende ontwerpvrijheid. Terwijl de technologie zich blijft ontwikkelen, kunnen we alleen maar anticiperen op de volgende spannende hoofdstukken in de geschiedenis van lassen.
Average Rating